JAPAN'S PREFERENTIAL TRADE STATUS
입력 2019.07.29 (14:59)
수정 2019.07.29 (16:45)
읽어주기 기능은 크롬기반의
브라우저에서만 사용하실 수 있습니다.
[Anchor Lead]
Now Japan only has to obtain cabinet approval before stripping Korea off its preferential trade status. Subsequently, Korean materials producers are stepping up their efforts to supply materials locally, without having to export it from Japan. But this doesn't seem too easy as the technological gap between Korea and Japan in the parts and materials sector is too wide, and local development requires much funding. Here is a look at some of the companies that are working furiously to produce the needed materials within Korea.
[Pkg]
A factory that produces essential materials for semiconductors. Workers must put on masks and dust-free garments then go through air shower before entering the production area. This is where photo resist applied on the semiconductor circuit boards is produced. Photo resist is among Japan's list of export control items. This company has devoted 30 years to the R&D and production of that material. However, it has minimal presence in the domestic market since the firm started as much as 20 years later than its Japanese counterparts. Japanese companies control 90% of the global photo resist market. The PR for next-generation semiconductors are entirely from that country. The Korean government belatedly started assessing the situation.
[Soundbite] JOO HYEON-SANG(KUMHO PETROCHEMICAL) : "A study to assess demands is underway to procure equipment as quickly as possible."
The local firm has several obstacles to overcome. It needs about two or three years to catch up with the level of Japanese technology and more than 100 billion won just to purchase the needed equipment. What is the situation like for hydrofluoric acid, another restricted item? This is the only place in Korea that produces 99.9%-pure hydrofluoric acid. Korea's hydrofluoric acid dependence on Japan is 44%. Tests are underway to determine whether it can be replaced with locally-made material, but more time is needed to develop hydrofluoric acid with a purity level of over 99.999%. Fluorine polyimide used in foldable screens is another restricted item. Fortunately, a local company is ready to mass-produce this material, so the problem isn't as dire in this front. Materials companies are working hard to turn this crisis into an opportunity. But most agree that large conglomerates and the government must join them to build a long-term cooperative relationship to fundamentally deal with such problems.
Now Japan only has to obtain cabinet approval before stripping Korea off its preferential trade status. Subsequently, Korean materials producers are stepping up their efforts to supply materials locally, without having to export it from Japan. But this doesn't seem too easy as the technological gap between Korea and Japan in the parts and materials sector is too wide, and local development requires much funding. Here is a look at some of the companies that are working furiously to produce the needed materials within Korea.
[Pkg]
A factory that produces essential materials for semiconductors. Workers must put on masks and dust-free garments then go through air shower before entering the production area. This is where photo resist applied on the semiconductor circuit boards is produced. Photo resist is among Japan's list of export control items. This company has devoted 30 years to the R&D and production of that material. However, it has minimal presence in the domestic market since the firm started as much as 20 years later than its Japanese counterparts. Japanese companies control 90% of the global photo resist market. The PR for next-generation semiconductors are entirely from that country. The Korean government belatedly started assessing the situation.
[Soundbite] JOO HYEON-SANG(KUMHO PETROCHEMICAL) : "A study to assess demands is underway to procure equipment as quickly as possible."
The local firm has several obstacles to overcome. It needs about two or three years to catch up with the level of Japanese technology and more than 100 billion won just to purchase the needed equipment. What is the situation like for hydrofluoric acid, another restricted item? This is the only place in Korea that produces 99.9%-pure hydrofluoric acid. Korea's hydrofluoric acid dependence on Japan is 44%. Tests are underway to determine whether it can be replaced with locally-made material, but more time is needed to develop hydrofluoric acid with a purity level of over 99.999%. Fluorine polyimide used in foldable screens is another restricted item. Fortunately, a local company is ready to mass-produce this material, so the problem isn't as dire in this front. Materials companies are working hard to turn this crisis into an opportunity. But most agree that large conglomerates and the government must join them to build a long-term cooperative relationship to fundamentally deal with such problems.
■ 제보하기
▷ 카카오톡 : 'KBS제보' 검색, 채널 추가
▷ 전화 : 02-781-1234, 4444
▷ 이메일 : kbs1234@kbs.co.kr
▷ 유튜브, 네이버, 카카오에서도 KBS뉴스를 구독해주세요!
- JAPAN'S PREFERENTIAL TRADE STATUS
-
- 입력 2019-07-29 15:02:20
- 수정2019-07-29 16:45:30
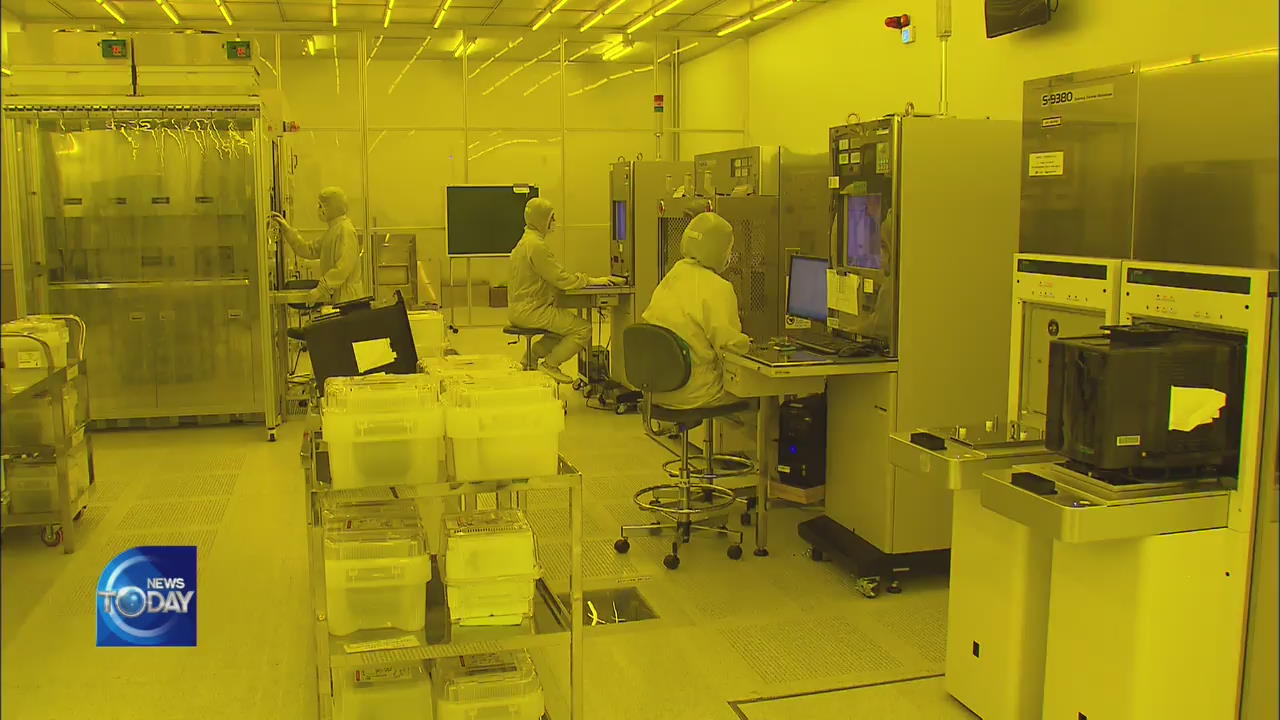
[Anchor Lead]
Now Japan only has to obtain cabinet approval before stripping Korea off its preferential trade status. Subsequently, Korean materials producers are stepping up their efforts to supply materials locally, without having to export it from Japan. But this doesn't seem too easy as the technological gap between Korea and Japan in the parts and materials sector is too wide, and local development requires much funding. Here is a look at some of the companies that are working furiously to produce the needed materials within Korea.
[Pkg]
A factory that produces essential materials for semiconductors. Workers must put on masks and dust-free garments then go through air shower before entering the production area. This is where photo resist applied on the semiconductor circuit boards is produced. Photo resist is among Japan's list of export control items. This company has devoted 30 years to the R&D and production of that material. However, it has minimal presence in the domestic market since the firm started as much as 20 years later than its Japanese counterparts. Japanese companies control 90% of the global photo resist market. The PR for next-generation semiconductors are entirely from that country. The Korean government belatedly started assessing the situation.
[Soundbite] JOO HYEON-SANG(KUMHO PETROCHEMICAL) : "A study to assess demands is underway to procure equipment as quickly as possible."
The local firm has several obstacles to overcome. It needs about two or three years to catch up with the level of Japanese technology and more than 100 billion won just to purchase the needed equipment. What is the situation like for hydrofluoric acid, another restricted item? This is the only place in Korea that produces 99.9%-pure hydrofluoric acid. Korea's hydrofluoric acid dependence on Japan is 44%. Tests are underway to determine whether it can be replaced with locally-made material, but more time is needed to develop hydrofluoric acid with a purity level of over 99.999%. Fluorine polyimide used in foldable screens is another restricted item. Fortunately, a local company is ready to mass-produce this material, so the problem isn't as dire in this front. Materials companies are working hard to turn this crisis into an opportunity. But most agree that large conglomerates and the government must join them to build a long-term cooperative relationship to fundamentally deal with such problems.
Now Japan only has to obtain cabinet approval before stripping Korea off its preferential trade status. Subsequently, Korean materials producers are stepping up their efforts to supply materials locally, without having to export it from Japan. But this doesn't seem too easy as the technological gap between Korea and Japan in the parts and materials sector is too wide, and local development requires much funding. Here is a look at some of the companies that are working furiously to produce the needed materials within Korea.
[Pkg]
A factory that produces essential materials for semiconductors. Workers must put on masks and dust-free garments then go through air shower before entering the production area. This is where photo resist applied on the semiconductor circuit boards is produced. Photo resist is among Japan's list of export control items. This company has devoted 30 years to the R&D and production of that material. However, it has minimal presence in the domestic market since the firm started as much as 20 years later than its Japanese counterparts. Japanese companies control 90% of the global photo resist market. The PR for next-generation semiconductors are entirely from that country. The Korean government belatedly started assessing the situation.
[Soundbite] JOO HYEON-SANG(KUMHO PETROCHEMICAL) : "A study to assess demands is underway to procure equipment as quickly as possible."
The local firm has several obstacles to overcome. It needs about two or three years to catch up with the level of Japanese technology and more than 100 billion won just to purchase the needed equipment. What is the situation like for hydrofluoric acid, another restricted item? This is the only place in Korea that produces 99.9%-pure hydrofluoric acid. Korea's hydrofluoric acid dependence on Japan is 44%. Tests are underway to determine whether it can be replaced with locally-made material, but more time is needed to develop hydrofluoric acid with a purity level of over 99.999%. Fluorine polyimide used in foldable screens is another restricted item. Fortunately, a local company is ready to mass-produce this material, so the problem isn't as dire in this front. Materials companies are working hard to turn this crisis into an opportunity. But most agree that large conglomerates and the government must join them to build a long-term cooperative relationship to fundamentally deal with such problems.
이 기사가 좋으셨다면
-
좋아요
0
-
응원해요
0
-
후속 원해요
0
이 기사에 대한 의견을 남겨주세요.